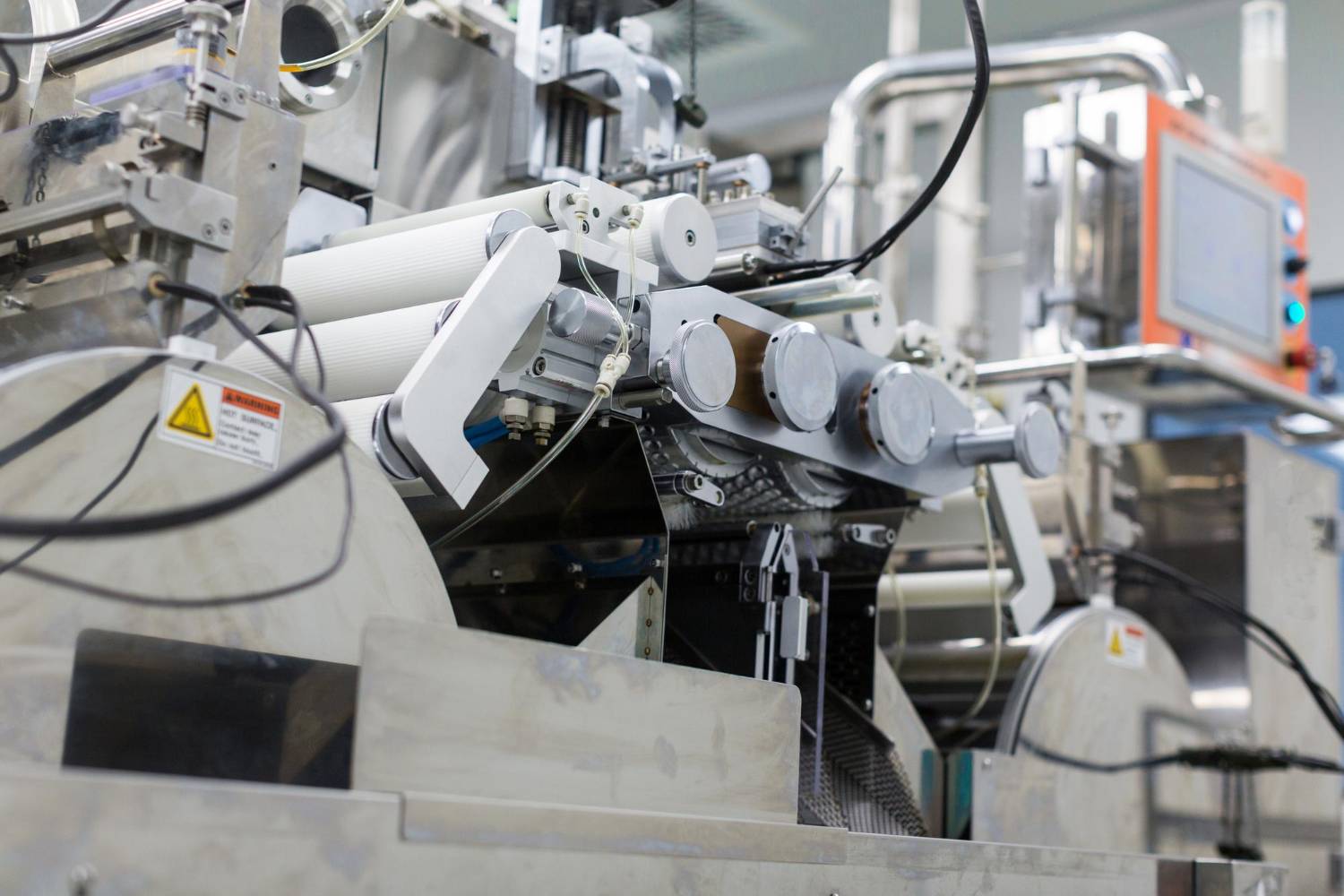
ABOUT US
Our Piezomotors Operate Based An A Newly Patented Technology
Founded in 2024, Piezo Motor Company is at the forefront of innovation in the design and manufacturing of piezoelectric motors. Headquartered in the USA, we have a global reach through a network of international distributors, delivering cutting-edge technology to clients worldwide.
Our team comprises highly skilled experts with extensive experience in piezoelectric motor and actuator design and physics. We are passionate about harnessing the unique properties of piezoelectric materials to create motors that offer unmatched precision, efficiency, and reliability. Our solutions are tailored to meet the diverse needs of industries ranging from medical devices to aerospace and robotics.
We pride ourselves on our commitment to excellence and innovation, continuously pushing the boundaries of what piezoelectric technology can achieve. Our dedication to research and development ensures that we remain leaders in this dynamic field, providing our clients with the most advanced and effective solutions available. Join us on our journey as we revolutionize the world of motion control with piezoelectric technology.
Technology & Innovation
Design Basis
Piezo Motor Company piezomotors operate based on new patented technology. Electrical excitation of a rectangular piezoceramic body (resonator) induces simultaneously two independent longitudinal and bending ultrasonic standing waves in two perpendicular directions. This action generates elliptical vibrations at the resonator’s center, resulting in linear motion of the motor, which is passively in contact with the resonator body.
The resonator is designed to generate simultaneously a first order longitudinal mode of vibration along the width (frequency v1) and a bending mode of vibration along the length (frequency v2). Within the oscillator assembly the combination of the two orthogonal modes of vibration create elliptical movement of the resonator contact site. Motion occurs as the result of frictional force between the contact site and rotor/liner slide.
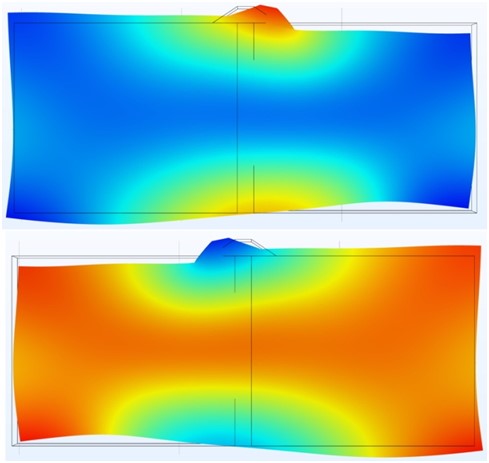
Electronic Driver PCB’s
Piezo Motor Company has developed an economical user-control interface (driver PCB) for use with our range of piezomotors. The primary purpose of the driver PCB is the formation of electrical pulses with specific frequency and amplitude for excitation of the piezomotor. Each driver PCB is factory programmed for use with the specified motor model to provide optimization of drive signals and integrated controls. Piezo Motor Company driver PCB’s are available as either open-loop or closed-loop versions.
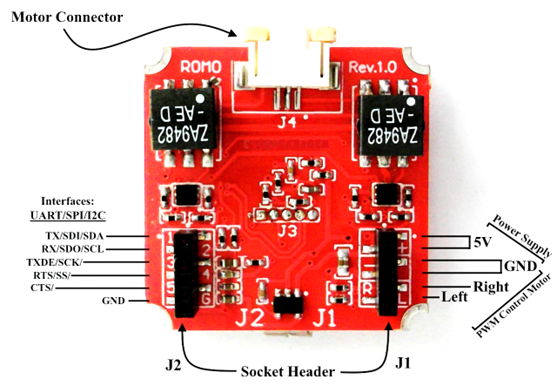
Open-Loop Driver
In open-loop, the driver PCB controls the motor as a standalone device without any positional feedback information. Motion control is implemented by applying a TTL-compatible PWM signal to the J1 external signal input connector located on the driver PCB. When either the environmental temperature or the load of the motor changes the driver PCB implements stabilization of the pre-programmed current. This provides maximum speed of movement according to the published motor specifications. Piezo Motor Company driver PCB has the ability to support the following interfaces:
- UART interface – The motor can be controlled by using UART commands through the pins 1,2,3,4,5,6 (TX,RX,TXDE,RTS,CTS,GND) of J2 connector.
- SPI interface – The motor can be controlled using SPI interface through the pins 1,2,3,4,6 (SDI,SDO,SCK,SS,GND) of J2 connector.
- I2C interface – The motor can be controlled using I2C interface through the pins 1,2,6 (SDA,SCLGND) of J2 connector.
Note: Piezo Motor Company programs the driver PCB for the specific interface required and provides Instructions with a list of commands DIRECTION, START, STOP, OPERATING MODE (PWM, Continuous), PWM (setting). Manual control of the motor can also be performed by pressing either of the two Manual Control Buttons located on the upper side of the driver PCB.
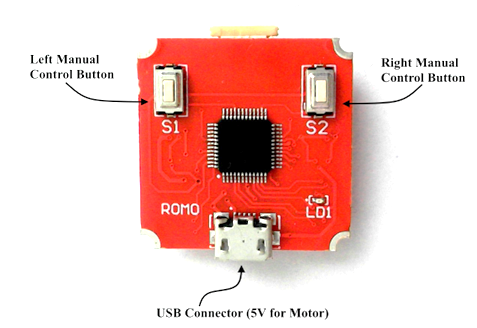
Closing the Loop with Factory-fitted encoder
Rotary Motors (the ROMO Series)
Piezo Motor Company ROMO series of rotary piezomotor with factory-fitted encoder use a magnetic encoder (Model ref. MagAlpha MA702). Users can monitor motor movement or close the loop (using PWM, UART or SPI or I2C control) by reading the signals directly from the encoder output.
Linear Piezomotors (the LRMO Series)
Piezo Motor Company LRMO series of linear piezomotor with factory-fitted encoder use an optical encoder (Model# iC-PX3212 from iC-Haus). As with the ROMO series, users can monitor motor movement or close the loop (using PWM, UART or SPI or I2C control) by reading the signals directly from the encoder output.